
| |
GN Electric Operations continued
Trolley Relay
The trolley relay is tripped by excess current to transformer
primary. These excess currents may occur from
(a) line surges on system, (b) Synchronizing surges on
locomotive, due to improper or premature operation of the
relays PR3 or SR. (c) Bouncing away of pantograph
from trolley line. (d) Any trouble on either the locomotive
transformer or synchronous motor, and even too heavy
a slack surge in train can jar any of the relays out.
Basically, the trolley relay is what is known as a lockout
relay. The trouble causes it (1) to trip off M-G set,
(2) after surge passes it lowers the pantographs. The
only troubles so far experienced with the relay itself has
been broken pigtail shunts, which can easily be found by
taking a jumper and paralleling around each separate
pigtail with the M-G start button held in. When you parallel
the broken wire, the M-G switches will close. Stick a
jumper around this to get over road. CAUTION: Jumper
only the broken wire, connecting jumper to the same
contacts wire is on.
Pantograph Relay
This relay is the primary circuit protection which takes
the place of the ground relay and trolley relay on the
General Electric cabs and no restraining devices must be
put on any contacts nor any adjustments attempted except
by authorized personnel.
In the event the PR relay operates due to a short circuit
or a ground, the PR relay light comes on in the operating
cab. To reset it is necessary to reset by hand. Remove
the cover over the relay box and lift the reset lever up in
a clockwise direction as far as it will go. This will reset
the control and open the pantograph down circuit, then
you can raise the pantographs and start the MG set the
same as the other General Electric locomotives.
The emergency switch is to be used only when the PR
fails to operate, or you think the engine should be killed
in a hurry.
M-G Overspeed Relay
This is a mechanical device operated by centrifugal force
from the R. P. M. of M-G set. It is calibrated to trip at
ten percent overspeed, or 825 R. P. M. Ordinarily it can
only be tripped in regeneration by loss of trolley power.
However, it can be jarred open by a heavy surge of train
slack, and in starting up M-G set, a blown carbon pile fuse
Page 61
will let the starting motor bring set up until overspeed
trips. Otherwise nothing but a ground or an open circuit
of its contact points will be troublesome electrically.
Relay PR3 operated by main exciter voltage closes at
600 R. P. M. to connect synchronous motor to transformer
by means of switches 3, 8, 9. PR3 sometimes fails to close
on account of a blown carbon pile fuse, or a broken spring
on carbon pile regulator.
OLR4 trips off synchronous motor when its full load
amperes are exceeded, throwing it back on reduced voltage
tap and opening JR circuit breakers, causing M-G set to
run on switches 1, 2, 3, 8, 9. This relay also trips when
any surge occurs, or pantographs bounce away from trolley
line. The only way it can fail, or give trouble, is a broken
pigtail shunt, or bad order contact, which will be evident
by synchronous motor switches pumping. They will change
from 4, 8, 9 to 1, 2, 3, 8, 9 to 4, 8, 9 and keep it up with
damage to themselves if not promptly shut down. If
pigtail is broken, put a jumper around the pigtail. Otherwise,
clean the contacts.
Relay SR controls the synchronous motor field switch
No. 10, which in conjunction with relay TDR1 synchronizes
M-G set with line. This relay SR is operated (1) its
contacts are held open by a D. C. pickup coil when M-G start
button is pressed, then after relay PR3 closes, connecting
synchronous motor to transformer, the A. C. coil of SR
holds contacts open and D. C. coil cuts out. These SR
contacts are held open by A. C. coil being energized by
slip frequency, which is induced in synchronous motor field,
and dies out to zero at full speed, when SR contact closes
No. 10.
The chief source of trouble with JSR has been mechanical
friction, in two ways:
(1) Either the relay was too stiff to close its contacts at
proper time (full speed) and its tension spring had to be
tightened, resulting in premature closing of contacts, and
by synchronizing M-G set too soon, causing trolley relay
to trip, lowering pantographs, or
(2) Insufficient tension in spring and contacts failing to
close at all, resulting in M-G set continuing to run on
reduced voltage tap, and switches 1, 2, 3, 8, 9 closed
instead of switches 4, 8, 9, 10. In either event trouble is
easily recognized by knowing M-G sequence and by applying
common sense, as (a) if pantographs come down just
as M-G set synchronizes (second bump), then SR is
Page 62
closing too soon. Hold it open for a few seconds longer by
inserting paper in its contacts, (b) If it does not close, then
close it by striking relay box. It is a very sensitive relay.
TDR1 is a magnetic type time delay relay, which is
bypassed by No. 10 in interlock, and caused to open in about
five seconds, changing synchronous motor over from the
reduced voltage tap to full voltage tap of transformer. It
seldom gives trouble, and at most, it may fail in two ways:
(1) If TDR1 has an open circuit and fails to close its
contact, everything will seem okay until SR closes No. 10.
Then 2, 5, 9 will open, and 4, 8, 9 close instantly without
the necessary time delay. The result will be to
synchronize too soon, trip trolley relay and lower pantographs. By
holding TDR1 in with a stick until a few seconds after No.
10 closes will get around this.
(2) If TDR1 sticks in mechanically, you can give bulkhead
door a kick and it will jar out and synchronize M-G
set, but when TDR1 sticks in due to either No. 10 not
closing, or a dirty interlock, or broken wire on No. 10 in
interlock, trouble will show up as: switches 1, 2, 3, 8, 9,
10 closed instead of 4, 8, 9, 10 closed. Cleaning the No. 10
in interlock will remove trouble.
TDR2 is the same type relay as TDR1. Its function is
to by-pass the A. C. overload OLR4 during the momentary
surge period as M-G set is being connected to transformer
and synchronized on line, as OLR4 would not protect
synchronous motor if it had to be set high enough so as not
to trip out during synchronizing period. After M-G set is
fully synchronized, switch No. 4 in interlock by-passes
TDR2, opening it. If TDR2 failed to close, it is probable
M-G set would not synchronize and switches would start
pumping, as explained in OLR4.
If TDR2 stuck in, M-G set would run okay, but engine
could not be moved as generator field switch No. 45 cannot
be closed unless TDR2 is out, or open. Neither would
synchronous motor be properly protected against damage,
as TDR2 in, shorts out OLR4.
Special Note: When "relay open or closed" is used in
text it is the air gap of relay you go by and not the
contacts, as most relays have double contacts. Some
contacts are making when relay air gap is open and, others are
open when air gap is open. '
Traction overloads OLR1, OLR2, OLR3, are operated by
the traction motor current and seldom give trouble, beyond
a dirty contact, or a broken pigtail shunt. They trip the
Page 63
JR breakers by de-energizing JR hold coil when they open
instantaneously. These relays are held contact closed by
spring pressure and are magnetically opened by overloads,
etc., on traction motors, which they protect.
Braking relay BR, is a two coil relay. (1) the D. C.
pickup coil holds relay closed and its contacts open when
"E" notch is taken on field or braking controller. (2) The
differential current coil holds the relay contacts open by
current from generators, until the regenerated current from
traction motors equalizes the generator current, and relay
opens, which closes its contacts, and automatically puts
engine in regeneration. These relays, if controller is left
too long on "E" notch, will burn out the D. C. pickup coil,
and engine cannot regenerate, unless started from
standstill in regeneration.
Another source of trouble on these relays: Should a bad
connection in regenerative exciter field circuit, or a blown
fuse in regenerative exciter field cause the differential
current coil to be energized too long by engine not promptly
getting into regeneration, while the controllers are set for
regeneration, then a burnout of differential current coil
will follow. Hence, if a cab fails to come into regeneration
within several minutes, especially one of a group, the
controllers better be shut off and try again. If cab still fails
to-regenerate, press red button and shut down cab before
burned out BR results.
VOLTAGE REGULATOR: (a) Reverse current relay.
(b) Carbon pile relay.
The voltage regulator is made up of two separate relays:
The reverse current relay is the familiar generator cut out,
same as on an automobile. It consists of a pickup coil
which closes the relay contact at a point where the exciter
voltage is slightly higher than the battery voltage, and a
differential current coil which bucks the pickup coil as M-G
set slows down and the exciter voltage drops below bat-
tery voltage. Then the battery current flowing back to
exciter through differential coil, by its bucking action,
causes relay contacts to open and cut out the exciter from
battery. Otherwise, the exciter would run as a motor on
battery and blow battery fuses.
The chief way failure occurs on RCR is failing to close
due to a broken resister tube, blown carbon pile fuse, or
failing to open due to welded contacts. If carbon pile fuse
is okay, relay may be closed and blocked in by hand, after
M-G reaches full speed. Otherwise, hands off, or you will
burn up the relay coils.
Page 64

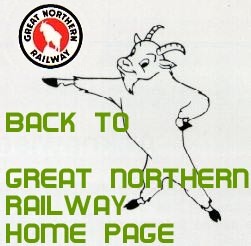 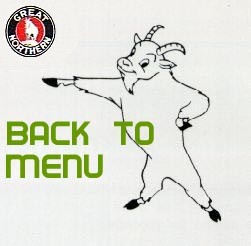
|